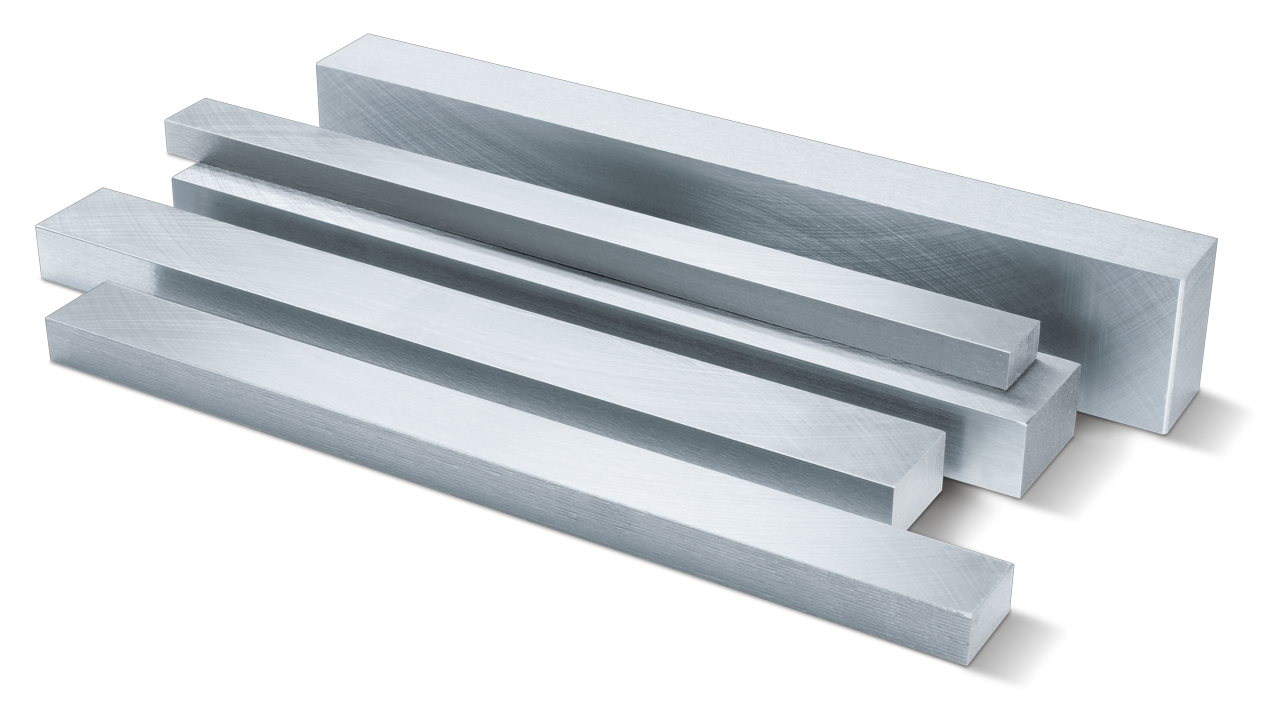
Shanghai Histar Metal provides high speed sheet, round bar and flat bar. High speed steel (HSS) is a subset of hardware prepares, usually used as cutting apparatus material.
It is frequently used in power-saw sharp edges and bores. This is stronger than the more experienced high-carbon steel devices that have been commonly used since the 1940s as they can handle elevated temperatures without affecting their strength (hardness). This property helps HSS to cut more quickly than high carbon steel, hence the term High Speed Steel. At room temperature, in there, for the most part, suggested heat treatment, HSS reviews, for the most part, show high hardness (above Rockwell hardness 60) and scraped spot opposition (by and large connected to tungsten and vanadium content frequently used in HSS) contrasted and normal carbon and device prepares.
Applications
The primary utilization of High Speed prepares keeps on being in the assembling of different cutting instruments: drills, taps, processing cutters, device bits, hobbling (gear) cutters, saw sharp edges, planer, and jointer edges, switch bits, and so on., despite the fact that use for punches and kicks the bucket is expanding.
Quick preparations have found a niche in fine hand devices where their relatively high longevity at high toughness combined with high scraped spot opposition rendered them appropriate for low-speed applications needing a sharp point, such as logs, etches, hand plane tops, and kitchen blades and folding knives from Damascus.
High speed steel devices are the most well-known for use in woodworking, since the level of production of the job beyond the edge is relatively fast for handheld tools, so HSS has a far longer edge than standard carbon steel devices.
Types
Quick formulations are amalgams that derive their properties from a number of alloying metals applied to carbon steel, typically like tungsten and molybdenum, or from a combination of the two, sometimes with separate compounds. They have a position in the multi-part composite structure Fe – C – X in which X refers to chromium, tungsten, molybdenum, vanadium or cobalt. The X category is usable for the most part over 7 percent, along with over 0.60 percent carbon.
Tungsten-type classes (e.g. T1, T15) in the unified numbering system (UNS) are assigned numbers in the T120xx structure, while molybdenum (e.g. M2, M48) and T113xx are middle of the road styles. ASTM values show 7 forms of tungsten and 17 forms of molybdenum.
The expansion of about 10% of tungsten and molybdenum altogether augments productively the hardness and sturdiness of High Speed prepares and keeps up those properties at the high temperatures created when cutting metals.
How can it Stay hard?
At the point when you think about a HSS cutting instrument, consider heat. The less warmth you make (in the device), the more drawn out an instrument will last. At the point when you heat treat HSS you take it to a specific temperature (now and again called high warmth) for a predefined time. This gives the HSS its definitive hardness, yet it’s extremely weak. Next its took to a temperature to “temper or draw” it. This is generally accomplished more than once. This carries the hardness to where you need it and gives the HSS sturdiness (both hardness and strength are controlled by the composite in the material). The Tempering temperature must not be surpassed in utilizing or honing the device or it will toughen (relax). This will differ from a couple of focuses (Rc) to a full downside. This is a very fundamental clarification of warmth rewarding HSS.
Shanghai Histar Metal Co., Ltd
Post time: Feb-16-2022